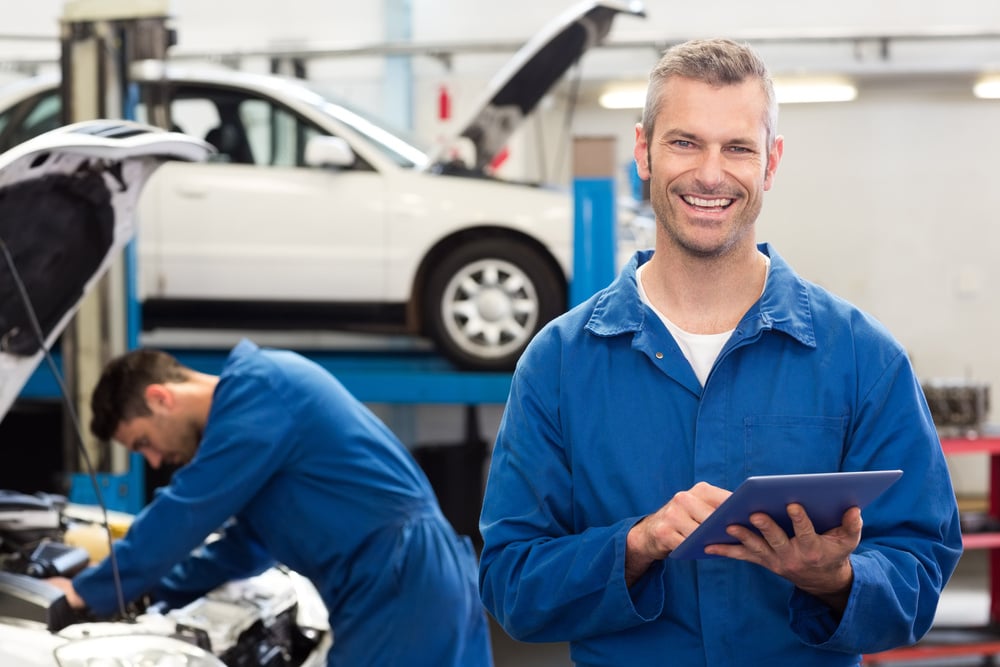
本事例のポイント
自動車メーカー様で稼働していた生産指示システムのサーバー老朽化に伴うシステムリプレイスのプロジェクトとなります。
リプレイス前のシステムでは国内工場/海外工場で異なるシステムを使っており、国内システムでも運用の違いから機能差、仕様差も大きかったため、それぞれに保守体制を構えており、システム維持・保守コスト削減、工場間の業務整理が課題となっていました。
そこで、システムリプレイスを機に各工場へのヒアリングを重ねて、機能統廃合によりグローバル標準パッケージとして作り変えることで、システムの維持・保守にかかるコスト削減と工場業務の改善を実現しました。
導入前の課題 |
・国内工場/海外工場のシステム差異によるシステム維持・保守コストが増大していた |
・工場間の運用差異による業務非効率が発生していた |
▼
課題解決の効果 |
・グローバル標準パッケージ化によるシステム維持・保守コストの削減を実現した |
・工場業務の標準化による業務効率の改善 |
背景・課題
システム差異、運用差異による機能・仕様の統廃合が課題に
生産指示システムの国内工場はIBM社のJES2機能の1つであるRJE(リモート・ジョブ・エントリー)で、海外工場は古いWeb基盤で構築されており、サーバー老朽化に伴いリプレイスが必要となります。
これらのシステムは画面の使い勝手、機能・仕様の差異は大きく、どのように標準仕様や機能・仕様の統廃合を進めていくかが大きな課題となっておりました。
解決策と効果
1年間の長い月日をかけた地道な仕様のすり合わせ
お客様と共に、現行のシステム機能・仕様や関連システムの基本仕様を整理し、新システムの画面共通標準仕様を作成し、丁寧にユーザーへの説明を実施しました。また、現行のシステムをソースレベルで解析し、細かい仕様の差異を洗い出し一つ一つ調整をすることで1年をかけて、新たにグローバル標準パッケージとして全ての画面仕様を確定させることができました。
その後は最大10名の体制で約1年6カ月で開発とテストを実施し、無事に第一号となる工場のシステム切り替えに成功しました。
今後の展望
世界中の全工場への新システム導入と機能改善
今後はお客様が保有する世界中の全工場の切り替えを進めていきます。
工場へのヒアリングを実施し、工場毎の運用に合わせてシステム設定をして導入することで、グローバル標準パッケージでありながら、工場の運用に合わせたチューニングを実施しております。
また、導入後の工場からも生産する自動車の変化に伴う、機能追加や改善の要望も出てきているため、並行して対応することで工場業務にマッチしたシステムの構築に引き続き尽力して参ります。